The pandemic woke companies up to the risks associated with distant, complex supply chains. This has more companies considering reshoring operations to the U.S., something that, along with making supply chains more resilient, may boost sustainability.
Reshoring is the process of returning the manufacturing of goods from abroad to the company’s original country. Only companies that have previously offshored operations have the ability to reshore.
“Due to the proximity of the supply chain network, reshoring is expected to positively impact the scope 3 carbon emissions from supplier transportation and distribution,” said Makarand Karanjikar, senior vice president of supply chain deployment at Schneider Electric.
Many companies that offshored decades ago to reduce production and labor costs started realizing they shouldn’t have done that between 2010 and 2019 “because prices had gone up a lot in China because wages have gone up rapidly,” Harry Moser, founder and president at the Reshoring Initiative, told FreightWaves.
Founded in 2010, the Reshoring Initiative is a nonprofit consulting firm aimed at bringing American manufacturers back to the U.S.
The pandemic along with geopolitical uncertainty have created more motivation for companies to consider reshoring in the past couple of years.
About 83% of manufacturers surveyed in 2021 said they were likely or extremely likely to reshore, a 29% increase from 2020, according to a 2021 report on the state of manufacturing in North America.
Motivations for reshoring
When China went on lockdown, huge factories and ports were left empty, and U.S. companies reliant on materials and products from China had no way to get them. Port congestion and skyrocketing shipping costs coming into the U.S. also made importing less attractive.
Karanjikar said the pandemic was “key in identifying vulnerabilities in supply chains and how prone they are to disruption.”
Now the Russia-Ukraine war and the tension between China and Taiwan are causing ripple effects and anxiety throughout global supply chains.
“Companies that were previously sourcing in China are very anxious to try to source closer to home at this point,” Rosemary Coates, executive director at the research and consulting organization Reshoring Institute, told FreightWaves.
These events have sparked companies’ planning efforts and strategies to keep more inventory on hand and either diversify sources of supply or reshore manufacturing operations.

Schneider Electric is aiming to have at least two sources for all of its critical parts and raw materials by the end of 2023.
“We have eliminated our dependence on any single country or region to avoid any geopolitical risks, and we are also driving some specific regionalization programs to shorten our supply chain and to manufacture close to our customers,” Karanjikar said.
Reshoring supply chains often:
- Makes them more agile and resilient to global risks and disruptions.
- Lessens the impacts of volatile ocean freight costs and port congestion.
- Reduces emissions from shipping and from production.
- Lowers the risk of major pollution and child labor because companies have more transparency.
- Appeals to more consumers because they prefer domestically made products.
“There’s a common preference for goods that are manufactured in your home country,” Coates said, adding that the majority of consumers would be willing to pay up to 20% more for domestically made products.
Supply chain visibility and emissions
Shifting operations from abroad back to the U.S. can lower greenhouse gas emissions in two ways: from avoiding emissions associated with shipping goods long distances overseas and from reducing emissions associated with production.
“The shorter you make that transportation cycle, the more you reduce your carbon footprint … and transportation costs,” Coates said.
Moser said production-related emissions are much higher in China than they are in the U.S., especially for products that require a lot of electricity. This is because China relies more heavily on coal to create electricity, and coal is a very carbon-intensive way to produce electricity.
“It’s pretty clear that especially in the developing countries, those [production-related] emissions, on average, are greater than they are in the U.S.,” Moser said. “If you assume people are going to buy a certain amount of stuff, is it better to do it here with less pollution than do it there with more pollution and with the pollution associated with shipping it?”
Bringing supply chains closer to home can also give companies more control over their operations.
“If you are sourcing from overseas somewhere, you don’t really have control over those companies. So you can’t enforce environmental or sustainability requests in the same way you could enforce them in the U.S. with your own production,” Coates said.
That lack of control and visibility could lead to more pollution and human rights issues such as child labor, Moser said.
“Domestic supply chains are more transparent than offshore and less polluting, cutting the world’s environmental impact by up to 25%, depending on the product,” stated a Reshoring Initiative report.
The report said companies that are considering reshoring are thinking about the sustainability impacts 32% more in 2022 than they did in 2021.
A company’s ability to measure and make changes related to environmental and social performance is more difficult for products made increasingly far away, according to a 2016 study about the link between sustainability and reshoring. Distance also makes it hard for companies to assess their suppliers’ commitment to sustainability.
The study said achieving sustainability goals is therefore “challenged by the global spread of suppliers.”
As the trend of moving operations closer to consumers continues, Moser predicted there will be fewer single large factories that ship things long distances and a larger number of slightly smaller factories that ship things more locally.
Reshoring EV batteries
Because the electric vehicle market is so new, the U.S. isn’t importing a large amount of them, Moser said. So although it prevents EV production from being offshored, building new EV factories in the U.S. isn’t considered reshoring.
“You can only reshore what you’ve offshored,” he said.
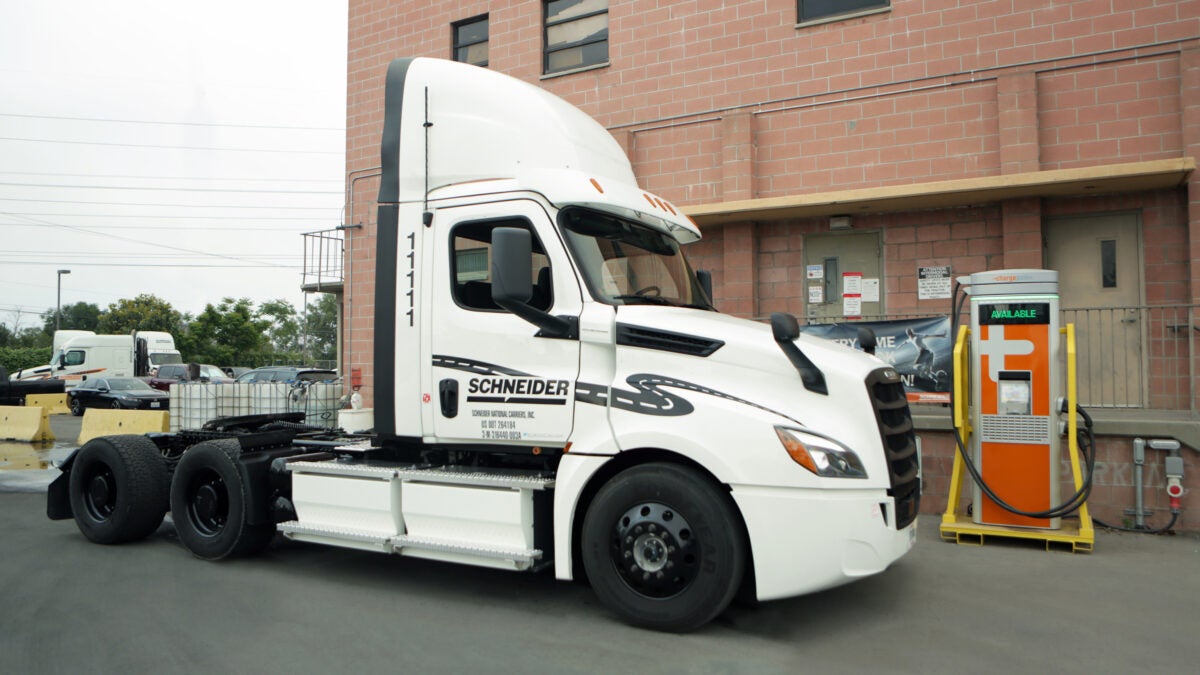
However, there is a large movement to reshore the manufacturing of batteries for EVs and semiconductors, which are used in vehicles and most electronic devices.
Chips are very small and light, so it doesn’t matter as much where they are produced, Moser said. The motivation to reshore their production is largely to ensure companies have access to the chips they need.
EV batteries, on the other hand, are “potentially dangerous” to ship, Moser said. “The batteries are expensive. They’re heavy. They could catch on fire, so my gut reaction is that it makes a lot of sense to produce them near the assembly plant where they’re going to be put into the car.”
A 2021 White House report on building resilient supply chains said China controlled an estimated 55% of the global capacity for rare earth mining and 85% of refining of rare earth metals in 2020. EVs and their batteries require large amounts of rare earth metals.
The report said the U.S. must secure supplies of critical minerals and metals “in a manner consistent with America’s labor, environmental, equity and other values.”
EV battery materials shipped to the U.S. from China would have higher production-related emissions because China’s electricity grid emits more carbon dioxide per megawatt hour of energy than in the U.S., according to the report. And there are significant costs and emissions associated with shipping them 7,000 miles to the U.S.
“We cannot afford to be agnostic to where these technologies are manufactured and where the associated supply chains and inputs originate,” the report said.
The Inflation Reduction Act (IRA) was signed into law in August, and it has incentives available for EV purchases. Some of the incentives hinge on a certain amount of raw materials being sourced in the U.S. or the final product being constructed in the U.S.
“These requirements will encourage automakers to reshore their materials to gain access to the credit, creating long-term impacts on the EV industry,” Karanjikar said. “We can expect to see an increase in the production of lithium iron phosphate batteries as the materials can be sourced locally in the U.S. and by countries within our fair trade agreement.”
He said Schneider Electric is looking for opportunities to start manufacturing EV chargers in the North American region for that market. The company also plans to ramp up local manufacturing in 2023.
The cost of reshoring
Higher wages and other production costs make it more expensive to produce many products in the U.S.
Moser said, compared to China, the average price from the factory is 40% higher in the U.S.
He said the Reshoring Initiative’s total cost of ownership (TCO) calculator helps companies analyze all of the relevant costs and risks associated with keeping operations where they are or bringing them back to the U.S.
If U.S. companies and governments focused on the TCO instead of the landed cost to evaluate where to source materials, 20% to 30% of imports would be replaced with domestically produced goods, Moser said.
The initiative is revising its TCO calculator to include carbon dioxide emissions. After a dollar amount for each ton of emissions is determined, the calculator will assign a carbon cost for every manufactured part.
Fighting high costs with automation
The Reshoring Institute can keep costs of reshoring back to the states to 15% more by relying heavily on automation, Coates said.
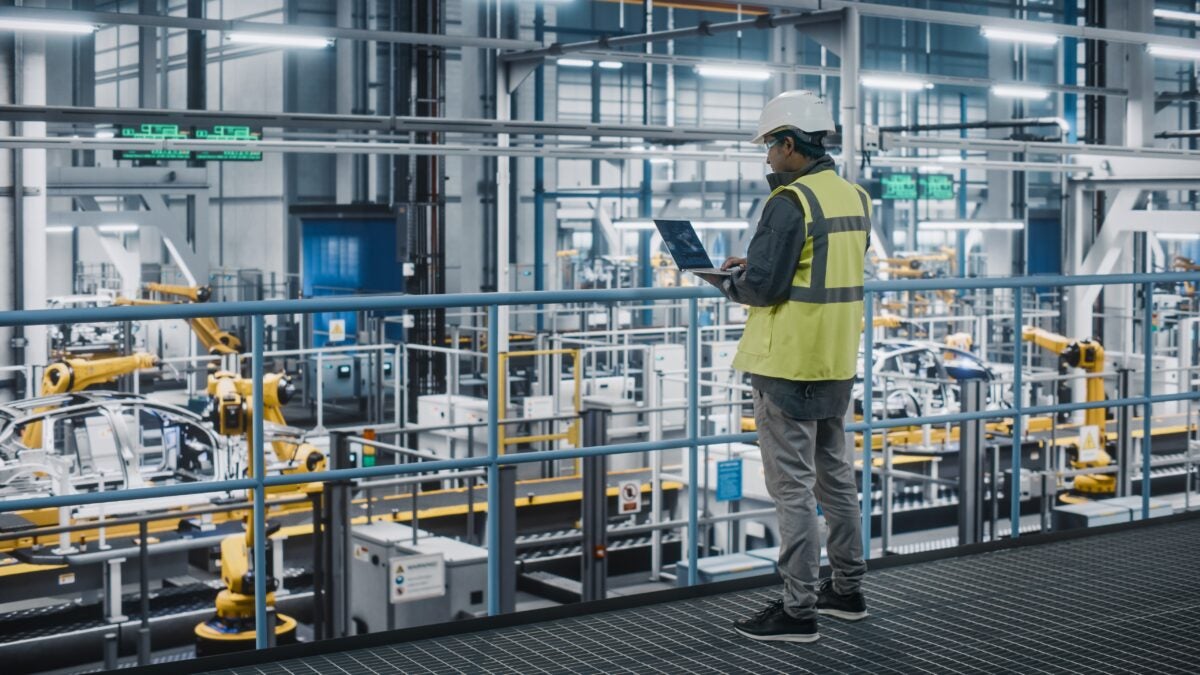
“It’s going to be essential that you either reengineer your manufacturing line or you fully automate the line because you have to extract labor costs out of the equation,” she said.
Schneider Electric is working to bring manufacturing closer to consumers through facilities in the U.S. and Mexico. Karanjikar said the company is able to “digitize energy management and industrial automation within our manufacturing facilities to measure our energy footprint [and] yield high levels of energy efficiency.”
But other countries like China and South Korea are automating faster than the U.S., so the U.S. would have to ramp up automation significantly just to remain at the current level of competitiveness, according to Moser.
A common criticism of automating factories as manufacturers reshore to the U.S. is that robots will take potential jobs. But many of the jobs that would be automated are either already automated in other countries or are labor-intensive, low-paying jobs.
“We don’t want those really low-paying, low-cost, highly labor-intensive jobs back in the U.S. because we just can’t afford it,” Coates said.
Any jobs that arise from reshoring are jobs that didn’t exist in the U.S. before.
Moser said the U.S. will lose more manufacturing jobs to automation in China or other countries than it will lose to automation that happens in the U.S.
Click here for more FreightWaves articles by Alyssa Sporrer.
Related Stories:
Can US cash in on reshoring manufacturing opportunities?
North America supply chain reshoring will not happen, report says
4 ways the Inflation Reduction Act could impact supply chains
Stephen Koehler
In the wake of the Pandemic, it has become increasingly apparent that supply chains are fragile things and the least disruption can cause ripples throughout industry. Similar actions happened in the wake of other disasters such as 9/11 or major natural disasters such as hurricanes striking the Gulf coast. Hopefully, once industry is willing to start reshoring manufacturing, local markets will become more robust and the good thing is that better paying manufacturing jobs will return to domestic markets. However, industry has shown a trend towards offshoring even with a reshoring strategy. Look for Mexico, Canada, Central America to get the lions pick of reshoring manufacturing. Connecting by truck is what will be the trend as industry, which considers Mexico and Canada the back yard of the US, will restore limited manufacturing to domestic markets. Industry has to realize that hollowing out the US domestic manufacturing capability accomplishes nothing but giving away good American jobs to offshore companies while the savings do nothing but create hollow shells of former manufacturing centers.
Sumit Wadhawan
In the background of covid ,it was evident that china +1 strategy had risen its head.
post COP21, sustainablity has finally got its seat on the table and the sooner big corporation start emphasizing this in their procurement budgets to actuals buying , this move will soon gather its required momentum.